Checking Out the Different Methods and Technologies Behind Plastic Extrusion
The realm of plastic extrusion is a blend of technology, precision, and technology, critical to numerous sectors worldwide - plastic extrusion. Advanced equipment, computerized controls, and a selection of materials converge in this complex procedure, creating high-quality, durable items. As the industry advances, a change towards lasting materials and intelligent machinery appears. The following conversation will clarify these techniques and innovations, while additionally meaning the interesting future leads of this critical manufacturing process.
Recognizing the Fundamentals of Plastic Extrusion
The process of plastic extrusion, commonly hailed as a foundation in the realm of manufacturing, forms the bedrock of this discussion. In essence, plastic extrusion is a high-volume manufacturing procedure in which raw plastic material is thawed and formed into a continual profile. It's a method widely utilized for producing products with a continuous cross-sectional account, such as pipes, window frames, and weather condition removing. The process begins with feeding plastic materials, often in the kind of pellets, right into a warmed barrel. There, it is warmed and mixed till it becomes molten. The liquified plastic is then required with a die, shaping it right into the wanted form as it solidifies and cools down.
The Duty of Different Products in Plastic Extrusion
While plastic extrusion is a commonly made use of method in manufacturing, the materials utilized in this procedure substantially affect its final output. Various kinds of plastics, such as polyethylene, abdominal, and pvc, each provide special buildings throughout item. As an example, polyethylene, recognized for its durability and flexibility, is commonly utilized in product packaging, while PVC, renowned for its stamina and resistance to environmental factors, is utilized in building. ABS, on the other hand, combines the most effective qualities of both, resulting in high-impact resistance and strength. The option of product not only influences the product's physical homes however likewise affects the extrusion rate and temperature. Manufacturers should meticulously consider the residential or commercial properties of the material to maximize the extrusion procedure.
Strategies Used in the Plastic Extrusion Refine
The plastic extrusion procedure involves various strategies that are important to its procedure and performance (plastic extrusion). The discussion will start with a simplified explanation of the fundamentals of plastic extrusion. This will be complied with by a failure of the procedure in detail and an exploration of techniques to enhance the efficiency of the extrusion technique
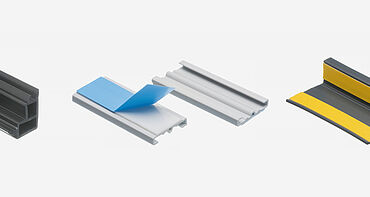
Recognizing Plastic Extrusion Essentials
In the realm of manufacturing, plastic extrusion stands as an essential process, important in the manufacturing of a wide range of day-to-day things. At its core, plastic extrusion entails transforming raw plastic material right into a continual profiled form. Fundamental understanding of these fundamentals allows for more expedition of the a lot more intricate elements of plastic extrusion.
Thorough Extrusion Process Break Down
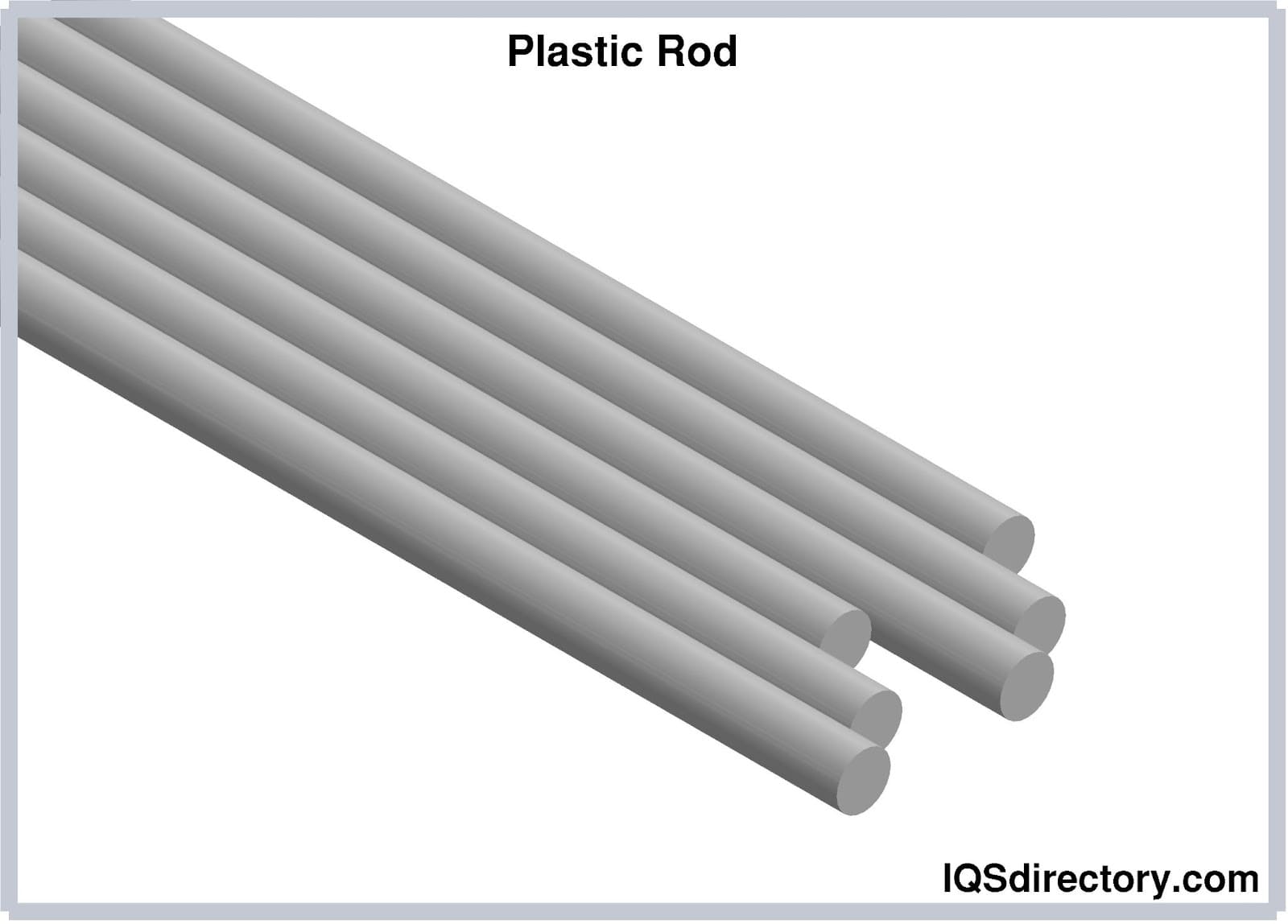
Improving Extrusion Technique Effectiveness
Performance gains in the plastic extrusion procedure can dramatically impact both the high quality of the final product and the general productivity of the operation. Continual optimization of the extrusion technique is essential to maintaining an one-upmanship. Techniques that improve performance often entail specific control of temperature and pressure throughout the procedure. Modern technologies, such as computerized systems and sensors, have actually been important in attaining this control. Additionally, making use of high-quality raw materials can minimize waste and enhance outcome top quality. Normal maintenance of extrusion equipment can also lessen downtimes, hence increasing efficiency. Lastly, adopting lean production concepts can help remove unnecessary steps in the process, promoting efficiency gains.
Exactly How Innovation Is Transforming the Face of Plastic Extrusion
The arrival of new technology has considerably changed the landscape of plastic extrusion. It has actually led to the advancement of sophisticated extrusion equipment, which has actually boosted the efficiency and top quality of the plastic extrusion process. Advancements in the extrusion process have likewise been driven by technical innovations, supplying enhanced capabilities and versatility.
Advanced Extrusion Equipment
Revolutionizing the world of plastic extrusion, advanced equipment imbued with sophisticated modern technology is ushering in a new age of effectiveness and accuracy. These equipments, equipped with innovative attributes like self-regulating temperature control systems, guarantee optimal problems for plastic processing, thus minimizing waste and enhancing item quality. While these improvements are currently exceptional, the continual development find here of technology assures also higher leaps ahead in the area of plastic extrusion equipment.
Technologies in Extrusion Procedures
Utilizing the power of modern innovation, plastic extrusion processes are undertaking a transformative metamorphosis. Developments such as electronic mathematical control (CNC) systems now enable more precision and uniformity in the manufacturing of extruded plastic. Automation better improves efficiency, decreasing human mistake and labor costs. The integration of expert system (AI) and maker knowing (ML) algorithms is revolutionizing quality control, anticipating inconsistencies, and boosting the general performance of extrusion processes. With the development of 3D printing, the plastic extrusion landscape is additionally increasing into new realms of opportunity. These technical advancements are not just boosting the high quality of extruded plastic items yet likewise thrusting the industry towards a more sustainable, efficient, and cutting-edge future.
Real-World Applications of Plastic Extrusion
Plastic extrusion, a reliable and flexible process, locates use in many real-world applications. The automotive market also uses this modern technology to produce components like trim and plastic bed linen. The strength and flexibility of plastic extrusion, paired with its cost-effectiveness, make it an essential procedure throughout numerous markets, underlining its extensive functional applications.
The Future of Plastic Extrusion: Patterns and forecasts
As we look to the perspective, it comes to be clear that plastic extrusion is positioned for substantial improvements and makeover. Green options to standard plastic, such as bioplastics, are likewise expected to gain traction. These fads show a vibrant, advancing future for plastic extrusion, driven by technical technology and a commitment to sustainability.
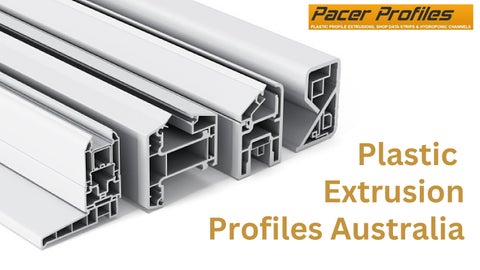
Final thought
To conclude, plastic extrusion is a complex process that makes use of advanced modern technology and differed materials to produce varied products. Technical developments, such as electronic controls, boost the manufacturing procedure and make certain regular results. Additionally, the market's focus on sustainability and intelligent equipment recommends a promising future. As plastic manufacturing continues to progress, it continues to be a vital part of lots of industries worldwide.
In significance, plastic extrusion is a high-volume manufacturing process in which raw plastic product is thawed and created into a constant profile.While plastic extrusion is a generally made use of technique in manufacturing, the products utilized in this process greatly influence its last output. At its core, plastic extrusion involves transforming raw straight from the source plastic material into a constant profiled form. It has actually led to the growth of innovative extrusion equipment, which has actually boosted the effectiveness and top quality of the plastic extrusion procedure.In verdict, plastic extrusion is an intricate procedure that uses advanced modern technology and differed materials to produce varied products.